Bolt Bell case study
Interest in gyms and workouts has increased by over 40% since 2020. To meet the growing demand for innovative fitness equipment, Bolt Bell developed ergonomically designed handles that fit your existing weight plates so you can create the perfect challenge for any workout.
hone.pd helped Bolt Bell redesign their existing 3D-printed product into a commercially viable, high-volume-manufactured product that delivers on price point and quality.
Bolt Bell's initial concept was a handle system that could adjust to fit existing weight plates, allowing users to create personalised challenges for any workout.
While the 3D-printed prototype demonstrated the product's potential, it faced several hurdles:
- High production costs associated with 3D printing
- Limited scalability for mass production
- Suboptimal design for efficient 3D printing
To evolve this innovative concept into a market-ready product without compromising its core benefits, our process included:
Design optimisation for manufacturing
We thoroughly analysed the existing 3D-printed design and identified elements causing high production costs and those incompatible with traditional manufacturing methods.
Our team then redesigned these components, ensuring they maintained functionality and were suitable for high-volume production techniques.
Material selection and testing
To address cost and durability issues, we conducted extensive research into various materials.
Our goal was to find an option that balanced cost-effectiveness with the strength and flexibility required for Bolt Bell's unique adjustable design.
Structural reinforcement
One of the key improvements we made was enhancing the overall strength of the Bolt Bell. By analysing stress points and usage patterns, we reinforced critical areas of the design.
This improved the product's durability and enhanced user safety, a crucial factor in fitness equipment design.
Optimising for 3D printing efficiency
While our main focus was on transitioning to high-volume manufacturing, we also recognised the importance of improving the current 3D-printed version. We re-oriented parts to optimise them for 3D printing, reducing material waste and printing time.
This interim solution allowed Bolt Bell to continue offering their product while we finalised the high-volume design.
Results and Impact
Our redesign of Bolt Bell yielded significant improvements across multiple fronts:
Cost reduction: By transitioning from 3D printing to traditional manufacturing methods, we dramatically reduced production costs, making Bolt Bell commercially viable for mass market distribution.
Enhanced quality: The redesigned product boasts superior strength and durability, ensuring a longer lifespan and better user experience.
Manufacturing scalability: Our design modifications allow for efficient mass production, enabling Bolt Bell to meet growing market demand.
Improved 3D-printed version: For the interim period, the optimised 3D-printed design offers better quality and efficiency, maintaining product availability during the transition to mass manufacturing.
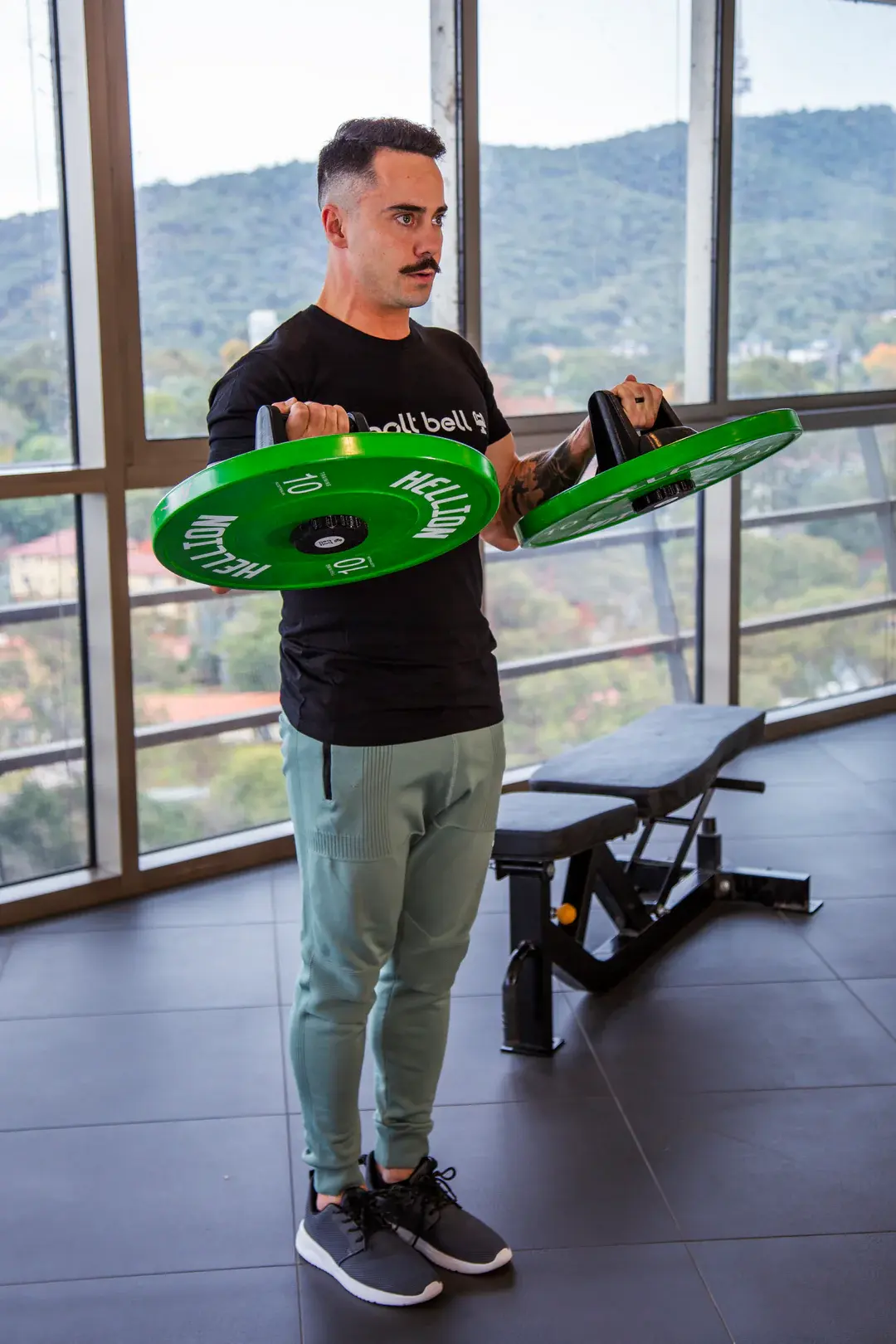
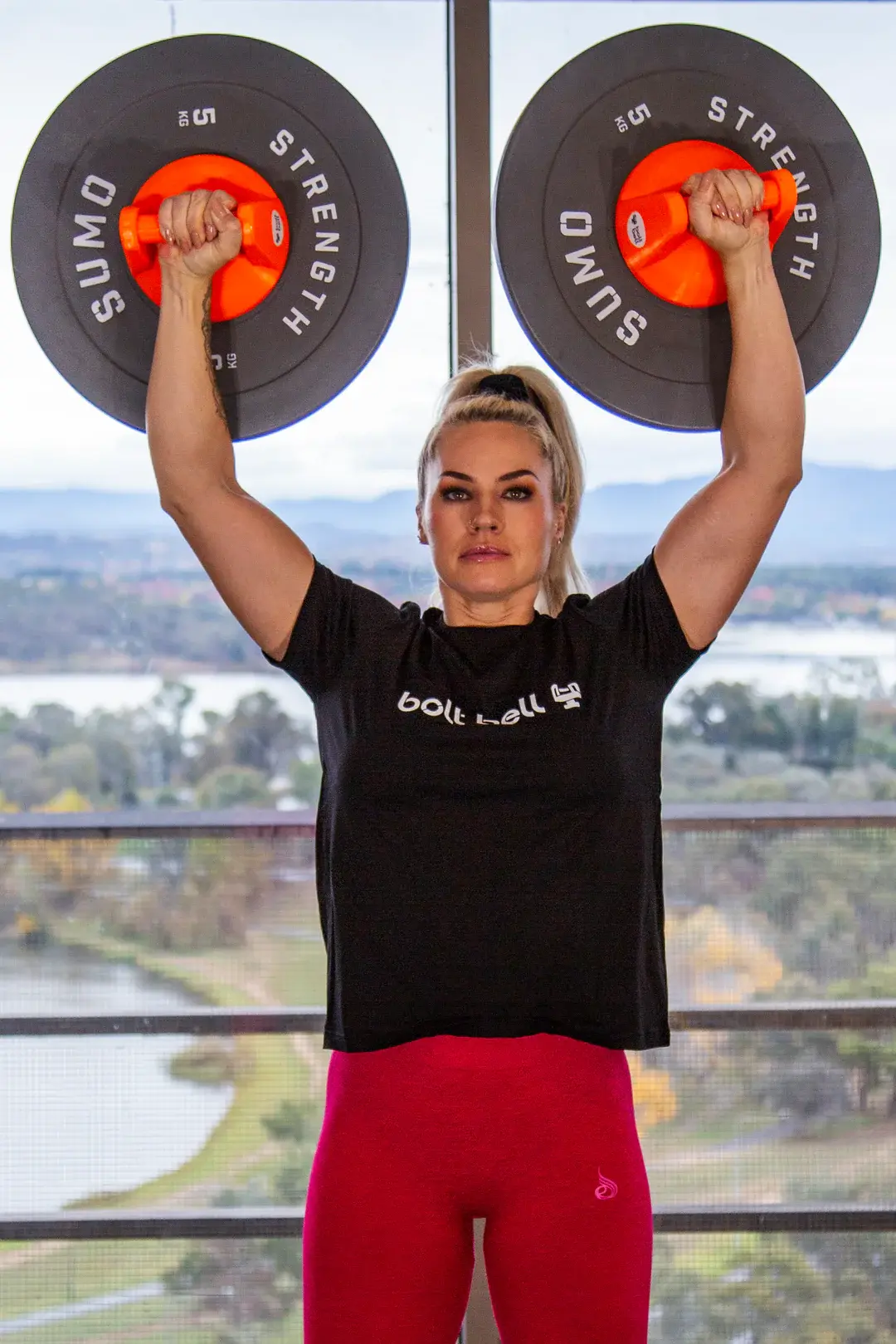
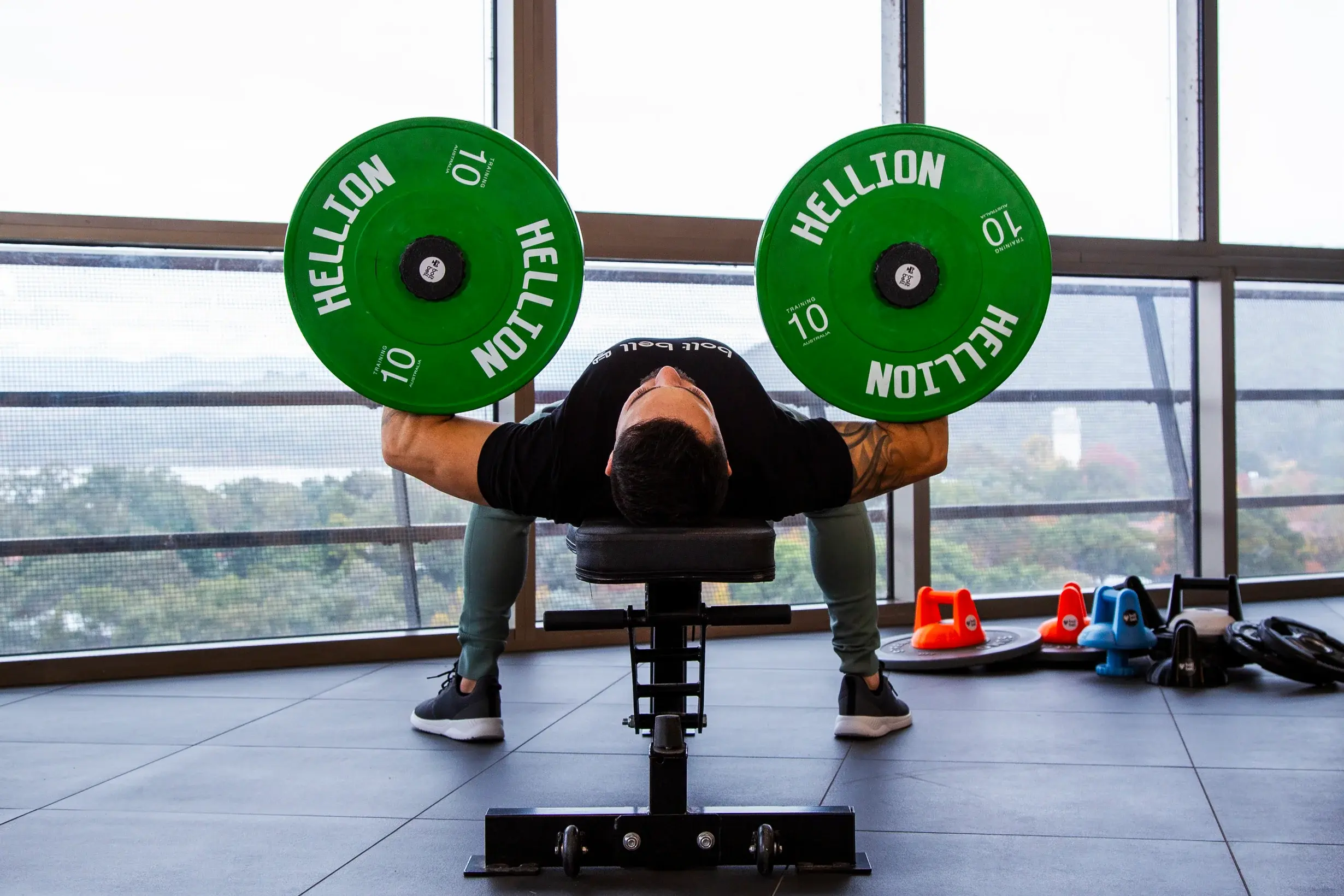
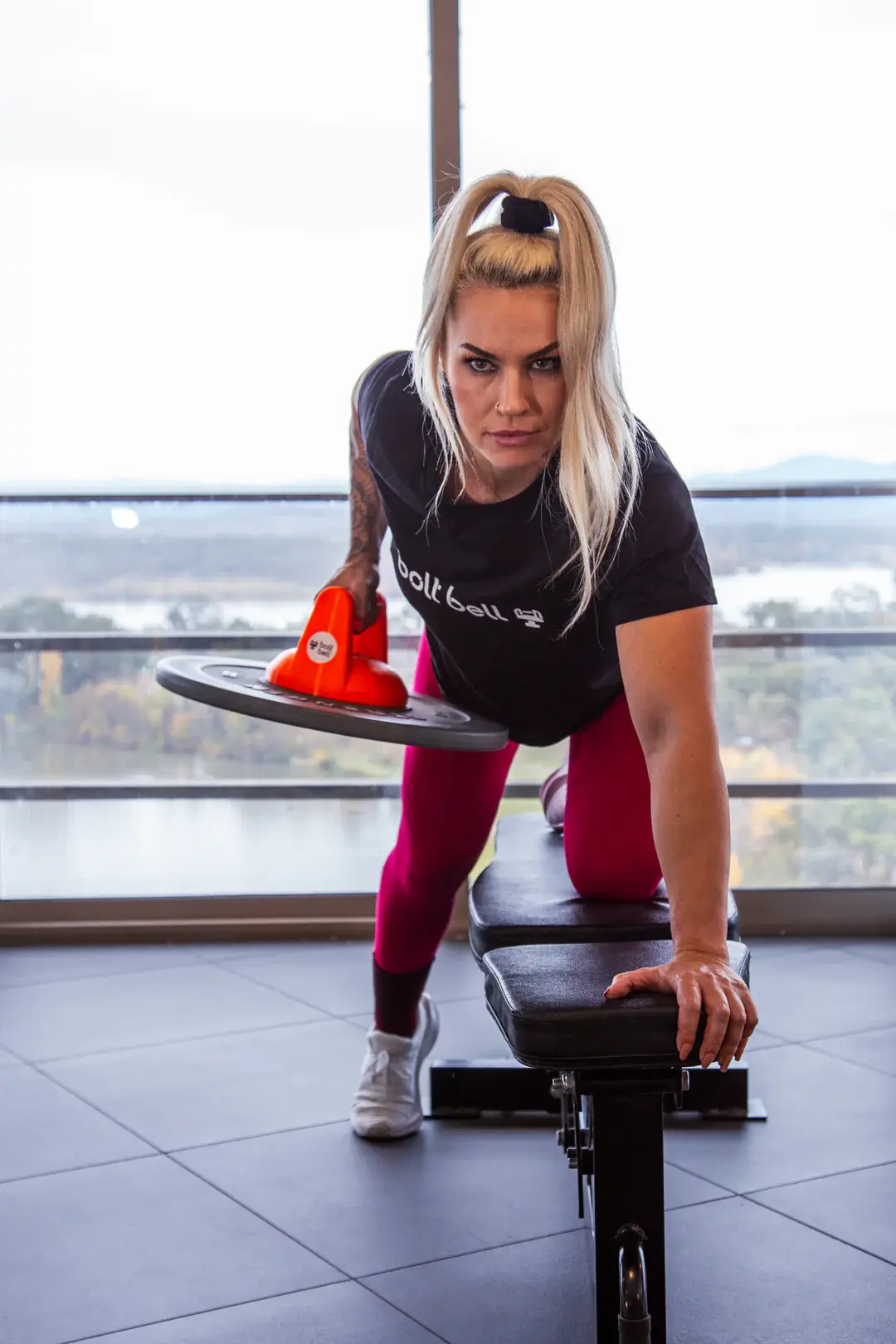
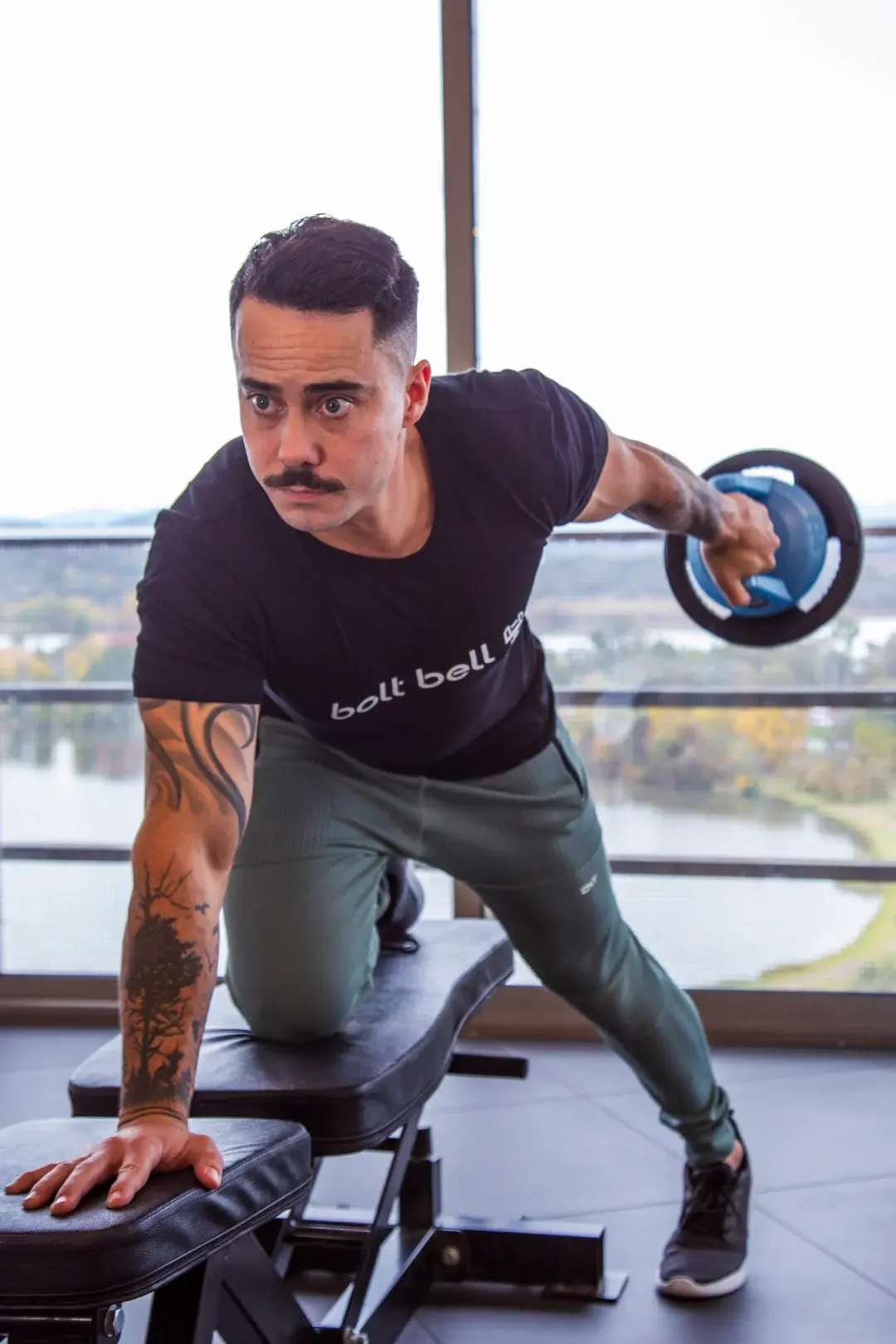
Conclusion
The Bolt Bell redesign is a perfect example of hone.pd’s ability to bridge the gap between innovative concepts and market-ready products.
By addressing the challenges of cost, quality, and manufacturability, we preserved Bolt Bell's ergonomic design's core benefits and enhanced its potential for market success.
Good design stands out. Get in touch with us today to kick-start your new product design project!