3D printing as a fabrication method allows for the easy construction of prototypes and organic forms that cannot be replicated using traditional manufacturing methods. The technology has been getting a lot of attention recently (even more than usual) thanks to wide media coverage of individuals and companies adopting printing to quickly adapt their production to supply Personal Protective and Medical equipment while there has been a worldwide shortage due to COVID-19.
Whilst 3D printing is an incredibly flexible method of manufacturing, producing items with commercial-grade machines is significantly expensive when compared to other methods of manufacturing. Because of the cost, it was reserved for producing prototypes, experimental product design or high-end designer pieces such as those produced by Joris Laarman labs.
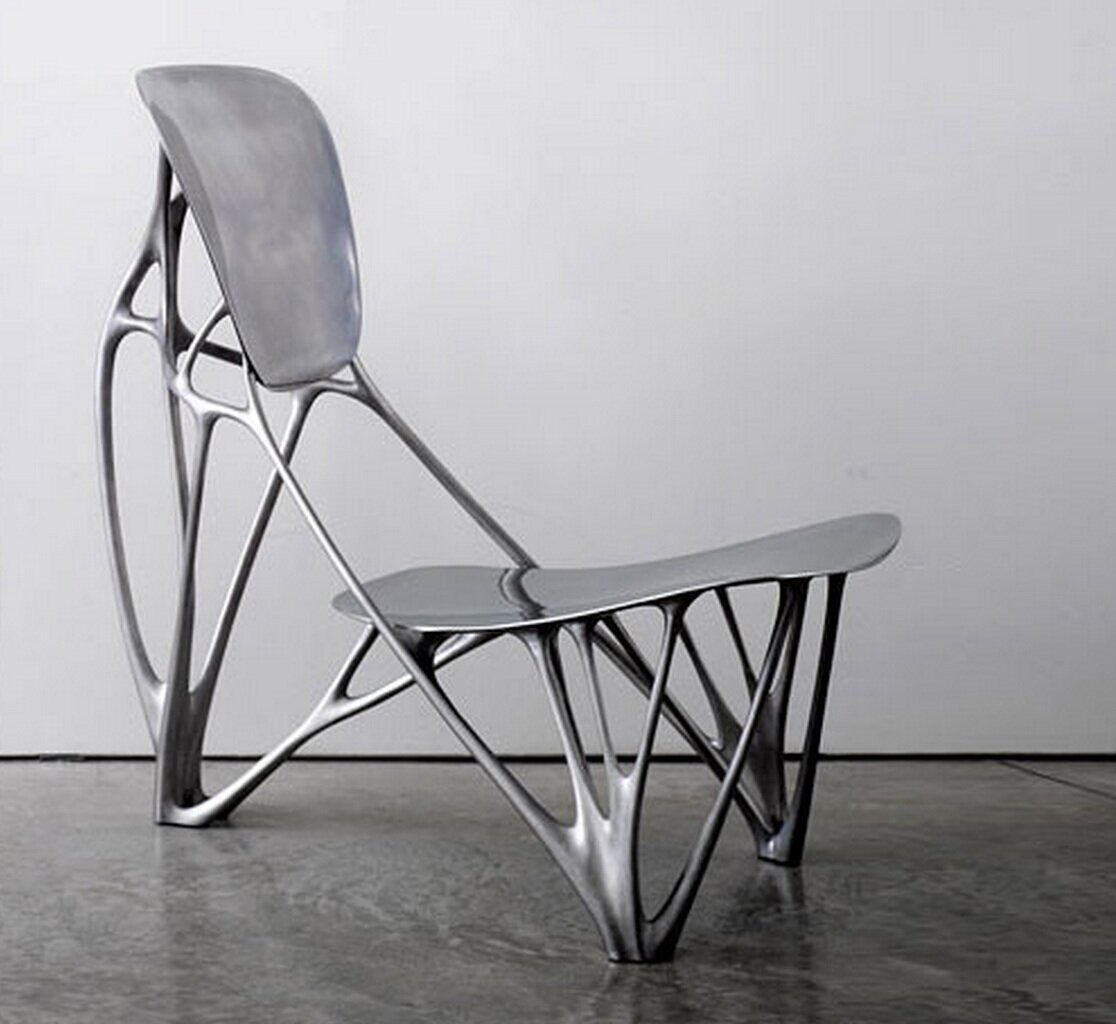
The bone chair by Joris Laarman Source:https://www.jorislaarman.com/
Joris Laarman has been producing furniture using 3D printing from its infancy. Starting with the bone chair using ceramic 3D printed moulds to build a chair cast in a single piece of aluminium and aided by Artificial Intelligence (AI) to design aesthetically pleasing, yet structurally sound supports.
In 2014 Laarman also designed the soft gradient chair, which was an experimental use of 3D printing polyurethane to replicate foam. The chair contains a mesh of cells that have varying densities depending on the localised structural requirements. This is achieved by leaving the cells open in areas intended to be flexible; and closed in areas that need to be rigid to support the user’s weight.
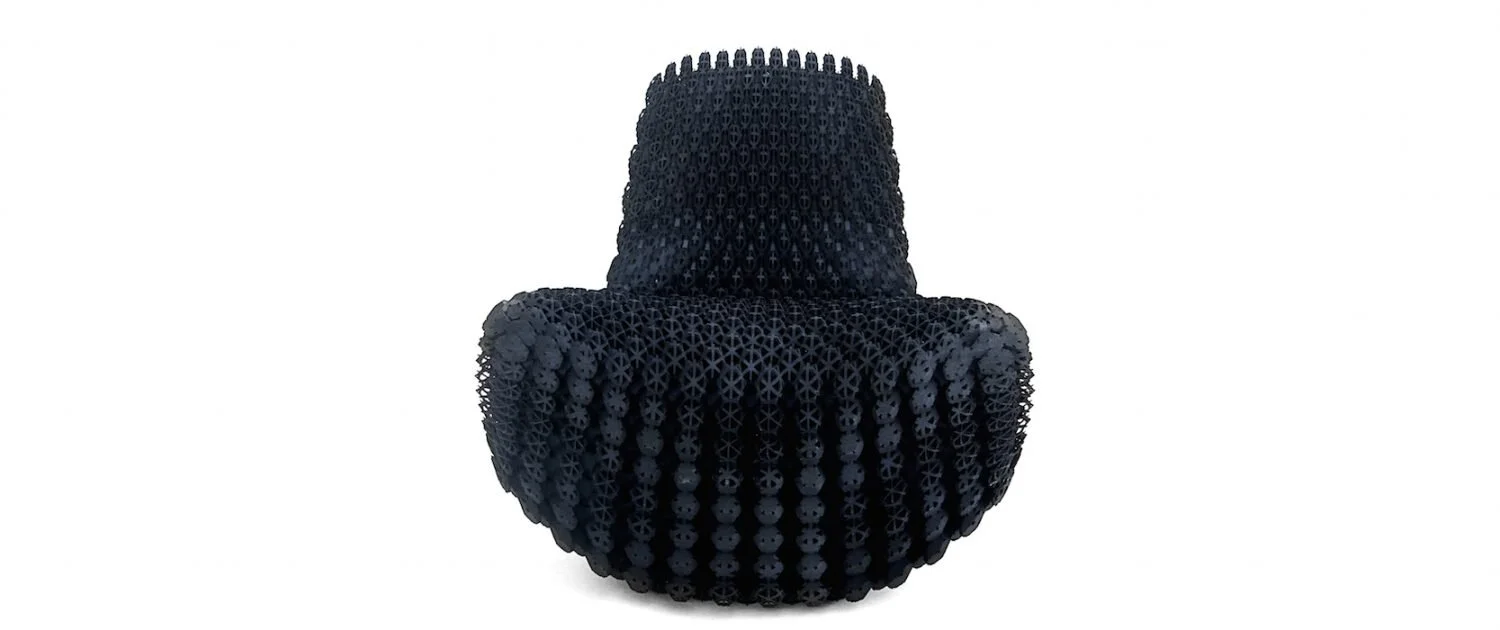
Soft Gradient Chair by Joris Laarman Source:https://www.jorislaarman.com/
While these great examples of the capability of printing to create unique product outcomes have been around for some time, on account of the previously mentioned costs, plus other factors such as limited range of materials, adoption of the technology has been extremely limited for mass production. This is now starting to increase with some exciting product outcomes.
One of the first products to grab attention with a mass producible 3d printed component was the 2017 Adidas Futurecraft line of sneakers, produced in partnership with Carbon3D, a technology company from California. The Futurecraft 4D range uses a 3D printed mesh midsole that has a variable density that increases from the heel to the toe. The shoe’s meshed sole is a complex extension of the AI generated forms adopted in the earlier described chairs. This is created via the Carbon3D technology which uses algorithms to find the optimum blend of material and geometry to create the shape which best supports the various dynamic loads applied to the sole of the shoe when being worn.
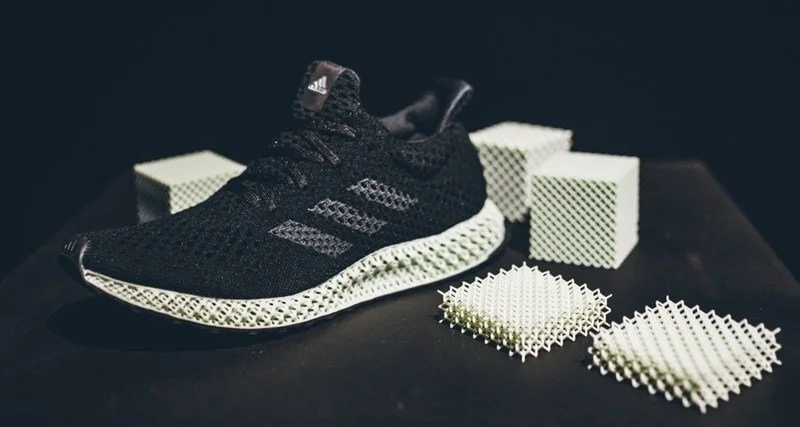
Adidas Futurecraft 4D using a 3D printed mesh by Carbon Source:https://boutique.humbleandrich.com/
Adidas are not the only sportswear brand utilising 3d printing technology to create the next generation of products, Following in their footsteps, Carbon are now also producing bike seats for Specialized and football helmets for Riddell, demonstrating the potential this technology has across a range of applications. Although still more expensive than other production methods, Carbon has been able to facilitate the mass production of 3D printed parts with their industry-leading UV resin printing technology, and make it affordable for select, premium range applications.
As opposed to the conventional methods of 3d printing SLS (selective laser sintering and FDM (fused deposition modelling); Carbon uses DLS (direct light synthesis) printing. DLS is much faster and can support a wide range of materials both rigid and soft.
Hone product design have been excited to have been collaborating with Carbon3D over the last 12 months working to design printed 3D meshes to enhance high performance foams for impact absorption in high impact products. If you have any interest in using AI to supplement Industrial Design, don’t mesh around; get in contact with hone product design Melbourne hello@honpd.com